Quality is the backbone of project success. In fact, poor quality management leads to 47% of project failures,1 causing delays, budget overruns, and stakeholder dissatisfaction.
This guide will walk you through the core principles of project quality management, exploring practical tools like Affinity Diagrams and PDPCs that help maintain high standards. With real-world case studies and actionable strategies, you’ll learn how to prevent costly errors and enhance stakeholder satisfaction.
Let’s get started!
What Is Project Quality Management
Project Quality Management includes the essential processes and activities needed to ensure a project meets its quality standards. This includes three key components: Quality Planning, Quality Assurance, and Quality Control, which work together throughout the project lifecycle.
Each stage plays a vital role in meeting stakeholder requirements and aligning with industry benchmarks. By embedding quality control measures early on, teams can spot potential problems, take corrective action, and maintain consistent performance.
In fact, recent research shows that organizations with strong quality management practices can cut rework costs by 30% and avoid delays that might jeopardize project timelines2.
Why Is Project Quality Management Important?
Because It Controls Project Costs: Effective project quality management helps control costs by preventing issues that lead to rework, delays, or even project failure. Studies show that companies using well-defined quality metrics see up to 20% improved cost efficiency by avoiding expensive rework and managing resources effectively3.
Because It Achieves Quality Standards: Defining and achieving quality standards ensures that a project meets both stakeholder expectations and industry benchmarks. A clear quality management plan allows project managers to track deliverables, implement corrective actions when needed, and deliver a final product meeting all quality requirements.
Key Components of Project Quality Management
Quality Planning
Quality Planning is the foundation of achieving project quality standards. It begins with identifying specific quality requirements for the project’s deliverables and establishing clear processes to meet those requirements. For insights on how forecasting can enhance planning accuracy, explore our guide on the power of forecasting methodology in project management.
Quality Planning usually involves:
- Defining measurable metrics
- Setting quality objectives
- Establishing procedures for monitoring quality throughout the project lifecycle
Documentation plays a crucial role in this phase. It ensures transparency, helps teams track progress, implements changes, and keeps stakeholders informed. For example, in a construction project, quality planning might involve setting guidelines for materials, workmanship, and safety standards. Proper documentation at this stage paves the way for consistent quality throughout the project.
Quality Assurance (QA)
Quality Assurance is a proactive approach focused on ensuring project deliverables meet defined standards by improving processes. Agility is one of the most common techniques for QA. Read this comprehensive guide on agile methodologies to learn how to streamline quality assurance in project management further.
QA aims to prevent defects through activities such as:
- Regular audits
- Process checklists
- Peer reviews
These measures help teams identify gaps early, make necessary adjustments, and maintain high standards. For instance, in software development, QA involves practices like code reviews and automated testing to prevent bugs and safeguard product quality.
▶️ Quality Assurance isn’t just about processes—it’s about teamwork. Strong team dynamics play a big role in catching issues early and maintaining high standards. For practical tips on building better collaboration, check out our article on effective team dynamics.
Quality Control (QC)
Unlike QA, Quality Control takes a reactive approach to identifying defects in actual deliverables. It involves inspecting, testing, and reviewing project outputs to ensure they meet established benchmarks. Key QC activities include:
- Regular inspections
- Product testing
- Review processes
For example, in manufacturing, QC might involve checking raw materials and finished goods to ensure they meet the required specifications. This ensures issues are addressed before delivering the final product to the client.
Tools and Techniques of Project Quality Management
Affinity Diagrams
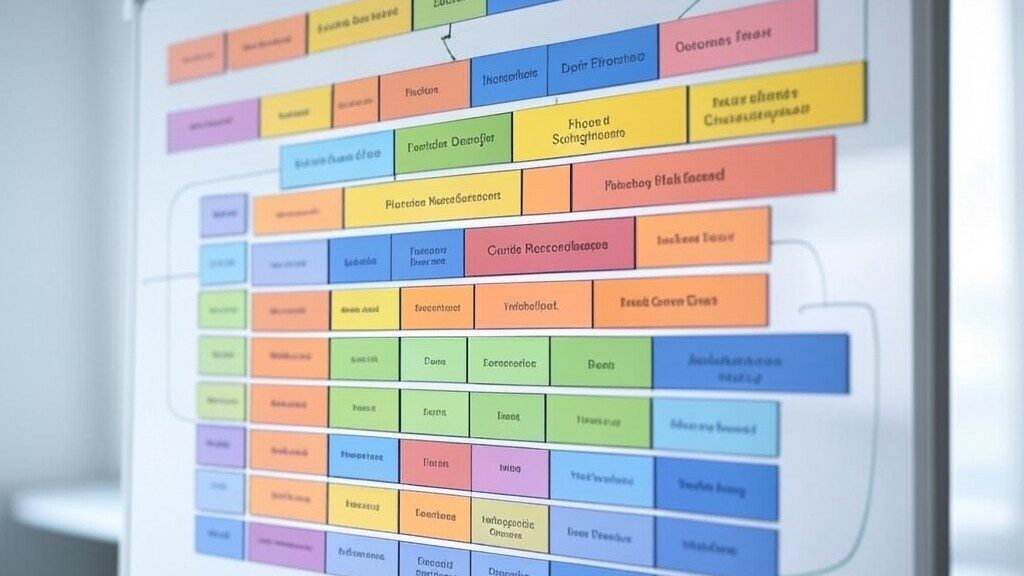
Affinity Diagrams are an effective way to organize large sets of ideas or data, particularly after brainstorming sessions. By grouping related concepts, teams can:
- Identify patterns
- Prioritize key issues
For example, a project manager might use an Affinity Diagram to categorize stakeholder feedback or organize potential project risks. This process makes creating a focused quality plan easier while fostering collaboration and innovation among team members.
Process Decision Program Charts (PDPC)
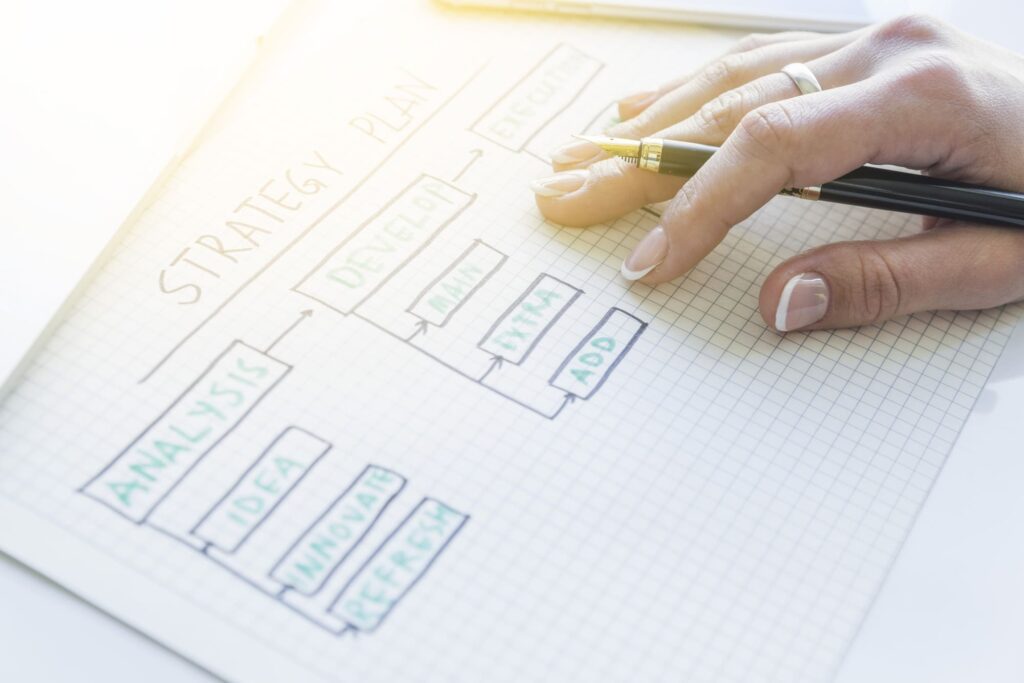
PDPC is a tool designed to anticipate potential challenges before they occur. By mapping out each stage of a project and identifying possible risks, teams can:
- Develop contingency plans
- Reduce the likelihood of costly disruptions
In software development, for instance, a PDPC can help anticipate risks such as delays in code development or hardware failures, ensuring the team is prepared to handle these obstacles effectively.
Interrelationship Diagrams
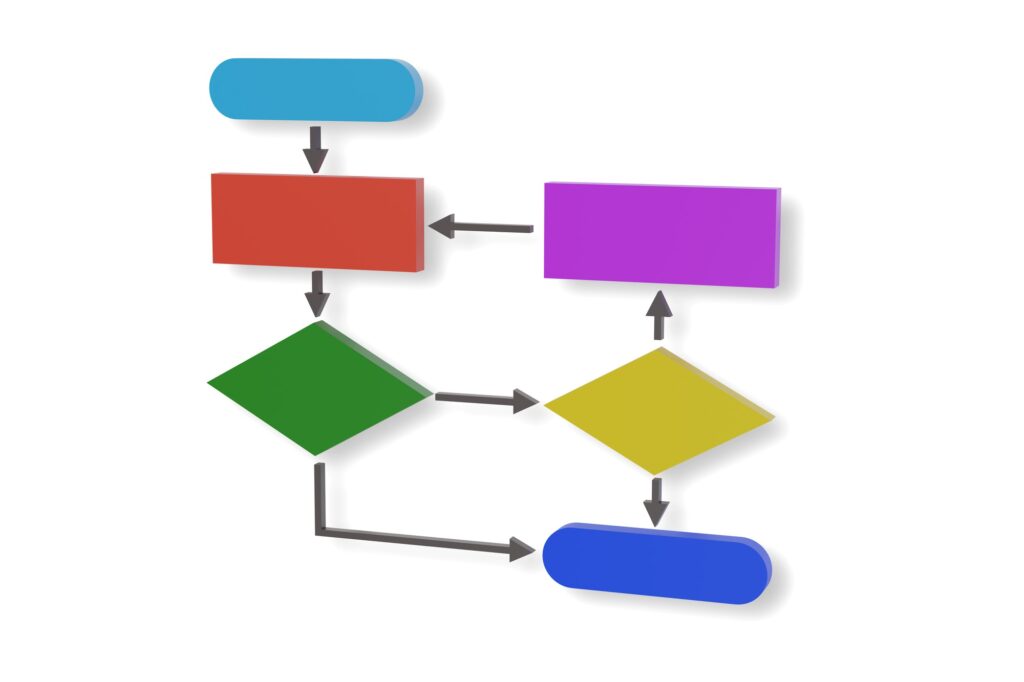
Interrelationship Diagrams help project managers understand the connections between different project activities. This is particularly useful in complex projects with many interdependent tasks. By mapping dependencies, managers can:
- Prioritize critical tasks
- Better allocate resources
For example, this tool can clarify the relationship between testing phases and product delivery schedules, ensuring that interdependencies are properly managed.
Prioritization Matrices
A Prioritization Matrix helps teams rank tasks or solutions based on criteria such as urgency, cost, or potential impact. This ensures that resources are directed to the most critical activities. For instance, in quality management, the matrix might prioritize final product testing over minor design adjustments to meet quality standards.
Network Diagrams
Network Diagrams visually represent project tasks, showing their connections and the critical path to project completion. These diagrams are useful for:
- Optimizing workflows
- Identifying potential bottlenecks
For example, in quality control processes, a Network Diagram ensures that quality checks are seamlessly integrated into the timeline, allowing teams to address issues before they escalate.
Matrix Diagrams
Matrix Diagrams visually represent relationships between various project elements, such as tasks, resources, and deliverables. They make it easier to identify areas needing improvement. For example, a Matrix Diagram in quality assurance can assess how testing phases impact product development, ensuring each phase meets required standards.
Challenges and Quality Project Management
Challenge | Description | Solution |
Integration of Quality Management into Agile Frameworks | Agile’s flexibility and rapid iterations may conflict with traditional quality assurance processes. | Embed quality checks into each iteration, implement continuous integration and automated testing, and promote a culture where quality is everyone’s responsibility. |
Managing Quality in Multi-Vendor Environments | Coordinating quality standards across multiple vendors can lead to inconsistencies. | Establish clear quality standards in contracts, conduct regular audits, ensure open communication, and use collaborative platforms to monitor quality metrics. |
Balancing Innovation with Quality Assurance | Innovation introduces uncertainties that challenge existing quality assurance processes. | Develop flexible frameworks, use pilot testing, and encourage cross-functional collaboration to evaluate innovative ideas from multiple quality perspectives. |
Ensuring Quality in Rapid Scaling Projects | Rapid scaling can strain quality management processes, leading to potential oversights. | Scale quality processes in tandem with growth, invest in scalable tools, train additional personnel, and regularly adjust quality management plans for project complexity. |
Addressing Quality in Complex System Integrations | Integrating multiple systems can cause quality issues due to incompatibilities and unforeseen interactions. | Conduct compatibility assessments, perform integration testing, maintain detailed documentation, and involve system integration experts. |
Maintaining Quality in Distributed Teams | Consistent quality across geographically dispersed teams is difficult due to cultural differences and communication barriers. | Create a unified quality management system, provide training, use collaboration tools, and schedule regular virtual meetings to align on quality objectives. |
Implementing Advanced Quality Metrics | Developing and utilizing sophisticated quality metrics to gain deeper insights into project performance. | Identify KPIs, use data analytics tools for quality data analysis, regularly review metrics for informed decision-making, and adjust metrics as project dynamics evolve. |
Key Considerations for Continuous Quality Improvement
Project managers must regularly evaluate key performance indicators (KPIs), such as defect rates or customer satisfaction, to ensure continuous quality improvement. Tracking these metrics enables teams to identify weaknesses and promptly implement corrective actions.
Another key consideration is team engagement. According to studies, involving employees in decision-making leads to higher project success rates. Teams should be encouraged to provide feedback on quality management processes and suggest improvements. This creates a culture of continuous improvement, where quality becomes a shared responsibility.
Real-Life Examples of Project Quality Management
1. Sydney Opera House
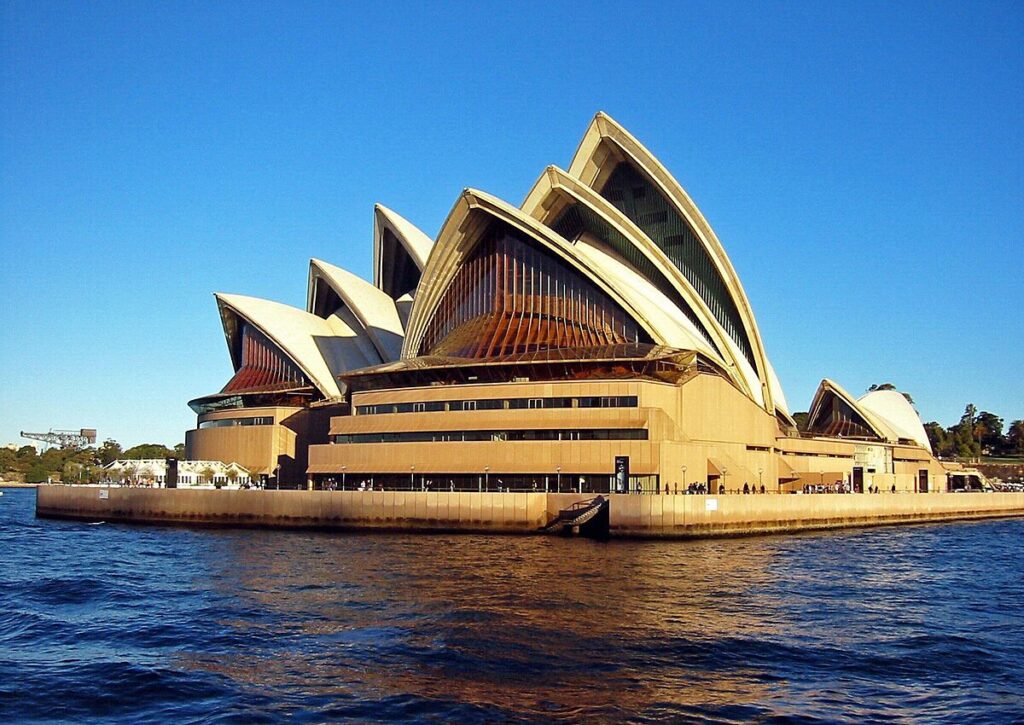
The construction of the Sydney Opera House4 stands as a testament to both the challenges and triumphs in large-scale project management. Initially estimated to cost AU$7 million and be completed in four years, the project ultimately took 14 years and cost AU$102 million, reflecting a 1,357% budget overrun.
Design and Engineering Challenges
Danish architect Jørn Utzon’s visionary design featured unique sail-like shells, presenting unprecedented engineering challenges. The original elliptical shell concept proved unfeasible, leading Utzon to develop a solution based on sections of a sphere inspired by peeling an orange.
Political and Managerial Turmoil
The project faced significant political challenges, particularly after a change in the New South Wales government in 1965. The new administration’s criticism of escalating costs and delays led to tensions with Utzon, culminating in his resignation in 1966. At that point, the shells were nearly complete, and costs had reached approximately AU$22.9 million.
Completion and Legacy
Following Utzon’s departure, Australian architect Peter Hall took over, making substantial changes to the interior design to meet new functional requirements. The Opera House was officially opened in 1973 by Queen Elizabeth II. Despite the project’s troubled history, the Sydney Opera House is now celebrated as a UNESCO World Heritage Site and an iconic symbol of Australia.
2. The Panama Canal Expansion
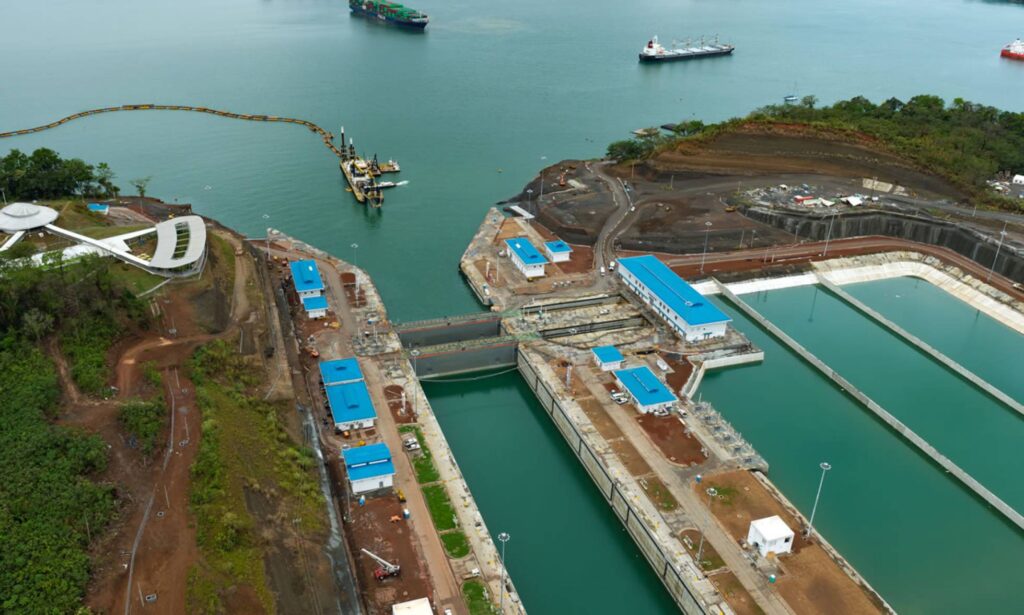
The Panama Canal Expansion5, known as the “Third Set of Locks Project,” was a monumental infrastructure endeavor aimed at enhancing the canal’s capacity to accommodate larger vessels and increase global maritime traffic. Initiated in 2007 and completed in June 2016, the project introduced a new traffic lane. It doubled the canal’s capacity, allowing the transit of New Panamax ships, which were significantly larger than their predecessors.
Challenges Faced
The expansion project encountered several significant challenges:
- Engineering Complexities: Constructing new lock complexes on both the Atlantic and Pacific ends required innovative design solutions to manage the increased size and weight of transiting vessels. Each lock chamber measures 427 meters in length, 55 meters in width, and 18.3 meters in depth, presenting substantial engineering demands.
- Geotechnical Issues: The diverse geological conditions along the canal route posed challenges, including varying soil compositions and seismic activity, necessitating comprehensive geotechnical assessments and customized construction techniques.
- Environmental Concerns: Ensuring the project’s sustainability was paramount. The expansion included the construction of water-saving basins to reduce water consumption per transit, addressing concerns about freshwater resource management in the region.
- Financial and Contractual Disputes: The project faced cost overruns and disputes between the Panama Canal Authority (ACP) and the construction consortium Grupo Unidos por el Canal (GUPC), leading to delays and requiring effective resolution strategies to keep the project on track.
Quality Assurance Measures
To address these challenges, the ACP implemented rigorous quality assurance frameworks, including adherence to ISO 9001 standards. Key measures included:
- Continuous Monitoring and Auditing: Regular inspections and audits were conducted throughout the construction process to ensure compliance with quality standards and to identify and rectify issues promptly.
- Stakeholder Engagement: Maintaining open communication channels with all stakeholders, including contractors, engineers, environmentalists, and the public, facilitated collaborative problem-solving and alignment on project goals.
- Risk Management: Comprehensive risk assessments were performed to anticipate potential obstacles, allowing for developing contingency plans and mitigation strategies to address issues such as geological surprises or technical difficulties.
Outcomes and Lessons Learned
The successful completion of the Panama Canal Expansion has profoundly impacted global trade, allowing for the passage of larger vessels and significantly increasing the canal’s capacity. The project underscores the importance of:
- Structured Quality Control Processes: Implementing standardized quality assurance measures is essential in managing the complexities of large-scale infrastructure projects.
- Effective Stakeholder Communication: Engaging all relevant parties through transparent and continuous communication channels helps align objectives and resolve conflicts efficiently.
- Proactive Risk Management: Identifying potential risks early and developing comprehensive mitigation plans are crucial in navigating the uncertainties inherent in large infrastructure projects.
3. Tesla Electric Car Project
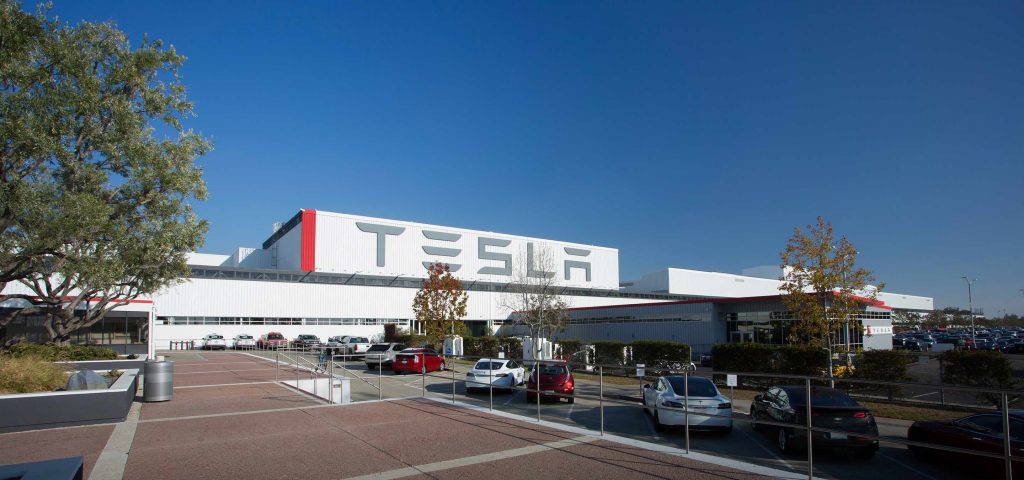
The development and launch of the Tesla Roadster6 marked a pivotal moment in the automotive industry, showcasing the potential of electric vehicles (EVs) to deliver high performance while adhering to stringent quality standards. Tesla’s project management approach during this period was characterized by innovation, extensive testing, robust risk management, and a commitment to continuous improvement through real-time feedback loops.
Tesla’s Quality Management Approach
- Agile Methodology: Tesla employed agile project management principles, emphasizing flexibility and rapid adaptation to changing conditions. This approach facilitated iterative development, allowing the team to make incremental improvements with each prototype.
- Iterative Testing: From the outset, Tesla implemented iterative testing to identify and address issues early in the product development cycle. This process enabled the company to refine the Roadster’s design and performance continuously, ensuring that each iteration met increasingly stringent quality benchmarks.
- Risk Management: The project faced significant challenges, including production delays and cost overruns. Tesla’s proactive risk management strategies, such as securing additional funding and revising production timelines, were crucial in navigating these obstacles and bringing the Roadster to market.
Challenges and Solutions
- Transmission Issues: Early prototypes of the Roadster encountered transmission reliability problems, with initial designs unable to withstand the high torque of the electric motor. Tesla addressed this by collaborating with multiple suppliers and ultimately developing a single-speed gearbox that met performance requirements.
- Financial Constraints: The ambitious nature of the Roadster project led to significant financial strain, bringing Tesla close to bankruptcy in 2008. Through strategic investments and a focus on innovation, Tesla overcame these challenges, setting the stage for future success.
Outcomes and Impact
The successful launch of the Tesla Roadster demonstrated that electric vehicles could compete with, and even surpass, traditional internal combustion engine cars in terms of performance. This achievement not only disrupted the automotive industry but also paved the way for Tesla’s subsequent models, such as the Model S and Model 3, solidifying the company’s position as a leader in the EV market.
Conclusion
Project quality management is an essential component of any successful project. By incorporating quality planning, assurance, and control processes, teams can ensure that their deliverables meet stakeholder expectations while aligning with industry standards.
We’ve seen how tools like Affinity Diagrams and PDPC help streamline the process, while real-world case studies from projects like the Panama Canal Expansion and Tesla Roadster demonstrate the power of structured quality management.
Maintaining high-quality standards reduces project costs, improves customer satisfaction, and increases the likelihood of repeat business. In a competitive market, quality is a key differentiator to make or break a project’s success.
To ensure your projects meet the highest quality standards, explore the tools and resources offered by Mirorim. Create a free account today and take the first step toward achieving project excellence with our quality management solutions.
References
- Pm. (2021, November 11). Project Failure Statistics: The Shocking Truth. PM 360 Consulting. https://pm360consulting.ie/project-failure-statistics-the-shocking-truth ↩︎
- Aragon, A., Makarova, E., Faure Ragani, A., Rutten, P., McKinsey & Co., Phil Duncan, & Anil Sikka. (2016). The great re-make: Manufacturing for modern times. In Operations as a Competitive Advantage in a Disruptive Environment. https://www.mckinsey.com/~/media/McKinsey/Business%20Functions/Operations/Our%20Insights/Manufacturing%20quality%20today%20Higher%20quality%20output%20lower%20cost%20of%20quality/Manufacturing-quality-today-Higher-quality-output-lower-cost-of-quality.pdf ↩︎
- MacAdam, T. (2009). Lean Project Management: Slashing Waste to Reduce Project Costs and Timelines. Paper presented at PMI® Global Congress 2009—North America, Orlando, FL. Newtown Square, PA: Project Management Institute. https://www.pmi.org/learning/library/lean-project-management-reduce-factors-6745 ↩︎
- Sydney Opera House: For Demonstrating Architecture’s Power to Refine a City (Most Influential Projects: #50) (2019). PM Network, 33, 94–95. https://www.pmi.org/learning/library/top-50-projects-sydney-opera-house-11757 ↩︎
- Wikipedia contributors. (2024, December 23). Panama Canal expansion project. Wikipedia. https://en.wikipedia.org/wiki/Panama_Canal_expansion_project ↩︎
- Business Insider India. (2021, July 26). How Tesla Went From Near-Failure To Stunning Profitability In Just A Few Years | Business Insider India. Business Insider. https://www.businessinsider.in/tech/how-tesla-went-from-near-failure-to-stunning-profitability-in-just-a-few-years/slidelist/39374469.cms ↩︎
One Response
Thank you guide! I found the breakdown of quality management tools very practical. How would you recommend balancing project deadlines with maintaining quality standards? Appreciate your insights!
There are free e-books with tons of advice in a Gen AI Free Toolkit for Project Managers that I recently came upon. I believe your readers would also benefit from it.